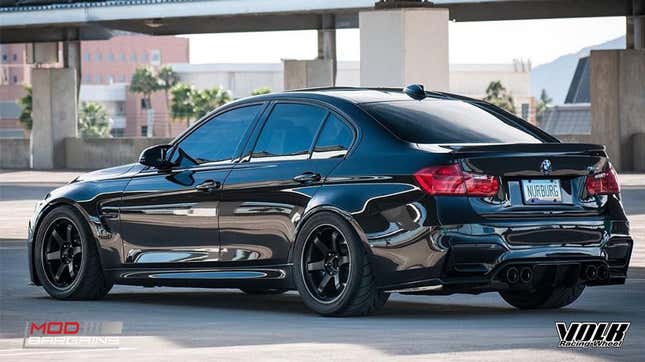
People spend a lot of time talking about forged wheels vs cast wheels. What does that mean, and why are forged wheels typically so much more expensive than cast ones? Is it because the traditionally unionized dwarf clans of the undermountain charge high hourly rates for their skills? Maybe, but actually, it’s because forged wheels start with better materials and undergo considerably more processes to reach their final form.
When you talk about really, really high-quality wheels, one name that comes up a lot is Rays Engineering. These Japanese-made wheels have built a reputation as being both exceptionally strong and incredibly light, and now, thanks to this rad “How It’s Made” style video, we know… well, we know how they’re made. Damnit.
Seeing the massive press smash hot aluminum like it was Play-Doh is unbelievably satisfying, as is seeing the kinds of complex shapes the manufacturer can achieve through multiple forging operations, including rotational forging to draw the barrel of the wheel down and form the lips of the wheel.
After the forging comes heat treating and then machining of the face, rounding of edges and deburring and drilling the bolt holes and valve stem hole. Then comes knurling and, maybe most interestingly, eddy current testing to non-destructively check for internal cracks or imperfections caused by the forging or heat-treating processes.
This video even goes into the design ideology employed by Rays. It’s a lot, but it’s the kind of thing that I find unbelievably interesting (and annoying but only because my broke ass can’t afford Rays wheels).